GIVE AND GAIN DAY 2019
November 8, 2019
Give and Gain Day 2019 saw Tridoor at Lixwm Primary School, Holywell. This years task was to help convert an un-loved out building into an outside classroom, decking and stage. We had the pleasure of installing a pair of patio doors, an electric awning and a decking stage area with handrails.
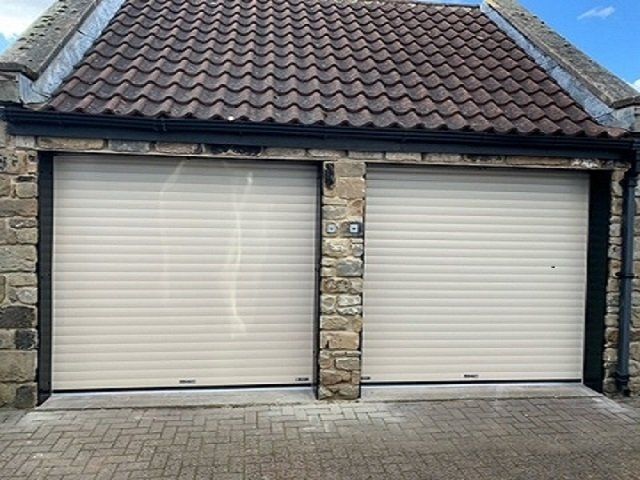
In simple terms yes. Roller shutter doors are manufactured using individual components that make up the full door system. The main components of a roller shutter door is the barrel assembly and the door curtain, these too are made up of individual items and can be replaced but the extent of this damage or wear to these two vital parts can sometimes make replacement a more cost effective option. The roller shutter door barrel: The barrel assembly or axle is often a steel tube, the size and thickness is determined to prevent deflection of the tube under the weight of the door curtain (industry standard is 1:400). The barrel may contain shafts, bushes, springs, motor and brakes. Depending upon the age of the door, all the items are readily available and replaceable. The roller barrel assembly is a classed as a suspension element and carries the weight of the roller shutter curtain, It is recommended that any repairs to the barrel assembly is carried out by a specialist door contractor who has the expertise to identify the parts, faults and can carry out the repairs safely. Replacement of motors and safety brakes should only be carried out by a specialist door contractor
In the design, manufacture and maintenance of industrial doors, demands of site, users and the environment are all taken into consideration. A suitable and sufficient risk assessment should be carried out for compliance and even where state-of-the-art requirements have been achieved, residual hazards are still present. Where recital 14 of the machinery directive is concerned, state-of-the-art is not cutting edge safety but the minimum level of safety required. Automatic doors can be opened by various means ranging from a simple push button, remote control, radar or induction floor loops, which activate the door and the door will raise to its upper most position. Once the door has reached its fully open position, for a fully automatic door, usually a timer is activated and the door will count down for a pre-determined time and the door will commence to close. An automatic door can also be where the door will remain at its fully open position indefinitely and requires a signal to close. Upon receipt of this signal, the door will begin to close automatically. For a door to work automatically in the closed position, safety features need to be present to prevent the door closing onto an obstruction or person. This can be in the form of a safety edge in conjunction with a low-level safety beam where either breaking the beam or contact of the safety edge will stop and return the door to the open position. Where a light barrier is installed, this is a full light curtain grid across the door opening and in the path of the closing door to a height of approximately 2500mm; crossing this beam at any point will stop and return the closing the door. As mentioned previously, recital 14 of the Machinery Directive relates to the minimum requirements for safety therefore residual hazards can still be present. When an automatic closing door is installed or maintained, the specialist door contractor should carry out a force test of the closing door. The force of the closing door should not exceed 400n, should reduce back to 150n in 0.75s to allow the door to stop and return so no overrun is present and should reduce further to 25n within 5s. The test is carried out at specific locations beneath the door and at heights where the door reaches full speed. A special force test meter is required to measure these forces on both doors and gates and should be calibrated on an annual basis. The test is recorded and a certificate is issued in order for the door to be compliant.